简介:欠平衡套管钻井作业,能够保证效率的同时,提升井眼的质量和安全性。
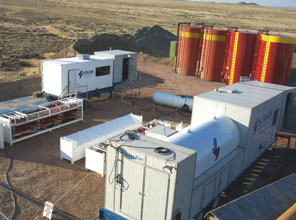
The underbalanced drilling package on one Rocky Mountain well included a rotating control head and four-phase separator.(Images courtesy of Tesco Corp.)
Underbalanced drilling (UBD) and its brethren technologies, managed-pressure drilling (MPD) and mudcap drilling (MCD), usually require significantly more planning and equipment than when drilling a “typical” overbalanced well. However, UBD provides many advantages, such as reducing or even eliminating some drilling problems, reducing formation damage and increasing rate of penetration (ROP). UBD results include improved recovery of reserves and better project economics due to higher ROP, faster drilling, and lower mud costs.
Casing drilling also results in high ROP and reduced drilling time and costs, as well as reduced formation damage. The technology has been used in numerous difficult wells to drill through troublesome well sections that would have been impossible with conventional drilling techniques. By reducing or eliminating lost circulation events, using casing to drill results in cost savings from reduced drilling fluid and lost circulation material, in turn reducing the environmental impact of the operation. Drilling with casing also results in significantly better borehole quality, reduced risk of wellbore instability, and reduced reservoir damage, resulting in better cement jobs, sometimes with significantly reduced cement volumes.
Combining drilling with casing with underbalanced drilling can result in even greater advantages. Underbalanced casing drilling (UCD) eliminates the need to kill and potentially damage or ruin the well to run casing after drilling with conventional methods. Additionally, UCD eliminates the need to trip drill pipe in openhole during a live well, increasing personnel safety and reducing potential environmental problems.
A history with UBD wells
Tesco Corp. has been involved in numerous underbalanced wells, including projects in South Texas and in the Rocky Mountains in Wyoming. Many of these underbalanced wells were drilled simply by installing a rotating control head (RCH), drilling ahead without weighting up the mud, and then flaring the gas. Drilling with an RCH may be a “poor boy” method but it points out the diversity of casing drilling that makes it so beneficial to this type of UBD approach.
In one Rocky Mountain well in Wyoming, Tesco drilled a directional hole section as well as an underbalanced section in the same well. The company was approached by an operator considering drilling with casing in an area known for substantial gas production in southeastern Wyoming. However, drilling these wells with conventional methods produced risks and challenges with numerous under pressured zones intermixed with abnormally overpressured zones that can lead to severe lost circulation problems, stuck pipe, sidetracks, and well control situations. The plan was to drill this well with 95⁄8-in. casing to 1,500 ft (457 m) measured depth (MD), then drill with 7-in. casing to about 9,600 ft (2,927 m) MD through several underpressured and overpressured formations. The 7-in. casing would be drilled directionally to horizontal at 4°/100 ft (30.5 m) with a rotary steerable system to 11,640 ft (3,549 m) true vertical depth ? 12,457 ft (3,798 m) MD.
The existence of subnormal and abnormal pressured formations had resulted in severe lost circulation problems, stuck pipe, and well control situations in previous wells drilled in the area. After drilling out the 7-in. casing shoe, the well was extended 2,000 ft (610 m) laterally into the zone of interest using UBD with a brine system. The underbalanced package included a rotating control head and four-phase separator.
The bottomhole assembly (BHA) was set and retrieved in underbalanced well conditions.
The 95⁄8-in. casing was drilled to 1,578 ft (481 m) MD with an 81⁄2-in. pilot bit. The 7-in. vertical section was then drilled with casing using a 61⁄8-in. pilot bit and 87⁄8-in. under reamer to 10,032 ft (3,059 m) MD at an average ROP of 48 ft/hr (14.6 m/hr). The directional assembly was picked up and the well was drilled underbalanced to 11,557 ft (3,523 m) MD with an average ROP of more than 31 ft/hr (9.5 m/hr).
The company’s casing drive system (CDS) was used to rotate and reciprocate the 95⁄8-in. and 7-in. casing during cementing operations to improve the cement bond.
In another Rocky Mountain well in Wyoming, the operator ended up drilling a section of the well underbalanced that had not originally been planned as such. The operator had planned to drill through sandy formation and hard shale rock. The plan was to drill a directional “S” curve well with 24° maximum angle and 2,000-ft departure to a depth of about 10,800 ft (3,293 m) MD. After drilling to section total depth (TD), the drillpipe would be pulled and the 7-in. casing would be drilled in using casing with a retrievable BHA. An 87⁄8-in. hole would then be drilled to finish the intermediate hole section down to a depth of around 12,500 ft (3,811 m) MD.
The CDS would be used and the BHA would be retrieved by wireline if the bit failed or when the well was finished. Although it was not planned as a UBD section originally, the operator ended up drilling the 87⁄8-in. section underbalanced.
The operator wanted to set the intermediate 7-in. casing string deeper in order to cross a troublesome weak zone of the formation. The company proposed that the well be drilled to the top of the trouble zone and wanted to finish the well by casing while drilling with a retrievable BHA system to the end of the intermediate section. Benefits of this plan included:
• Eliminating hole-conditioning trips;
• Reducing the chance for
lost circulation;
• Mitigating potential for stuck drillpipe;
• Reducing lost time;
• Mitigating stuck conventionally
run casing;
• Diminishing the potential for failure
to land conventional casing on
bottom; and
• Testing the under reamer in hard rock (greater than 20,000 psi ultimate compressive strength).
The CDS was used to make up, trip in, and rotate the casing. The BHA, with an aggressive polycrystalline diamond compact bit and proprietary under reamer, proved successful, drilling through numerous problem zones to TD at ROPs that equaled or exceeded the ROP in surrounding offset, conventionally drilled, wells.
The company’s Hydro-Form (hard faced, crimp-on) centralizers provided protection from wear on the casing and provided for stand-off during cementing. Hard-faced wear bands were also installed below each of the couplings to increase casing wear protection during rotation.
The hole section was successfully and safely drilled and cased with fewer mud losses than the offset, conventionally drilled wells, while also drilling in hard rock in an underbalanced environment. Fluid losses in the hole section were higher than anticipated although the operator expected that drilling with casing would cure fluid losses encountered. However, this turned out not to be the case in this well bore.
A rotating control head was installed by the operator and drilling went ahead without increasing the mud weight, allowing the operator to maintain a mud column in the annulus. Intermittent partial returns were experienced, leading the operator and company to believe that drilling the section underbalanced was “healing” the well bore while it was being casing drilled and allowing for the fluid column to build up. This eliminated drilling with the outside of the casing dry, reducing the chance of a twist off resulting from high friction rates.
Combining underbalanced drilling with casing drilling provides an operator with another tool. The versatility and flexibility of casing while drilling is illustrated by the successful performance of an underbalanced well section that was added to the well plan to mitigate fluid losses.
In addition to reducing or mitigating lost circulation problems, rig crew safety is significantly enhanced during drilling with casing operations by eliminating tripping drillpipe and running casing, particularly during underbalanced operations when the crew is dealing with a live well that is naturally flowing.
The versatility of UCD is one reason that several major oil and gas companies chose this method over drilling underbalanced wells with conventional drilling techniques.