简介:据估计,全世界40%的油藏需要进行防砂处理,如果不加以控制,则将会磨损生产管柱,加大油井维修作业量和成本。严重的情况下会导致油井完全停产,威德福公司在壳牌的膨胀管技术基础上,开发出的这套膨胀防砂管(ESS)技术,在各个油田现场的应用成功率达100%,包括在尼日利亚的一个水平部署。
An estimated 40%of the world’s reservoirs require sand control. Uncontrolled, sand production will wear out production string components and require frequent and costly workovers. In some cases,it can block production completely.Additionally,incorrect selection of a well’s sand-control method can drastically decrease the well’s production rates and cost-effectiveness.
To more effectively managedownhole sand production,Weatherford International’s Petroline unit, an Aberdeen-based company,developed Expandable Sand Screen(ESS) technology that builds on Shell’s patented expandable pipe technologies. To date,the technology has had a 100% success rate in a variety of field applications, including the first-ever horizontal deployment of an ESS in a reservoir in Nigeria.
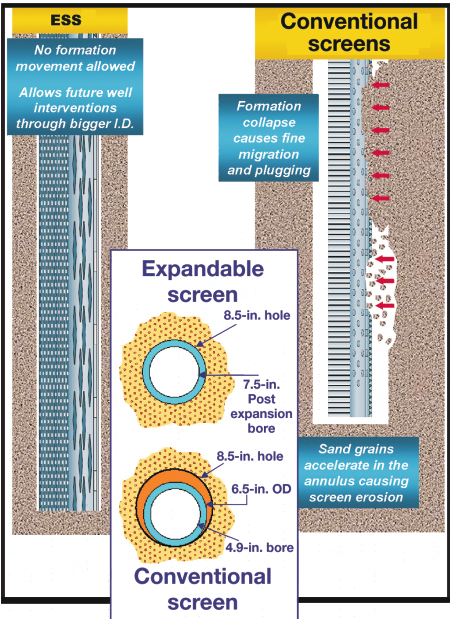
Sand control challenges. Traditional sand control technologies include gravel pack completions and stand-alone sand screens?but several limitations exist with these methods.Correctly placedgravel pack systems,for example,are good at controlling sand but they are depth filters and can eventually plug,reducing production.They are also expensive to install,andrequire many downhole hardware components and complex manipulations of hardware,sand and carrier fluids.
Non-gravel pack screens’limitations stem from the annular gap surrounding the screen to the borehole wall.In an unconsolidated formation,the borehole wall can collapse,mobilizing many particles and formation fines.This increase of produced particles and fines directly contributes to premature screen plugging that,in turn,leads to concentrated areas of flow,termed“hot spots,”where severe erosion can develop.
Expandability:A new option. ESS technology addresses many of the above-noted limitations due to its expandability component.The technology includes three elements:1)the slotted,expandable base pipe;2)over-lapping filtration membranes;and 3)an expandable outer protection sleeve.
The ESS expands when a taperedmandrel or cone is pushed,from the topdown,through the screen inner diameter,causing both inner and outer layers to conform to the required diameter.During this expansion phase of setting the screen,the overlapping filter membrane expands by one layer(ofthree),sliding radially andaxially over another until thefinal diameter is achieved,while remaining f irmlysandwiched between theother two layers.Provenbenef its of using ESS include the following.
Conformity to a variety of wellbores. The ESS canexpand by up to 100%of itsoriginal diameter,allowing itto conform to almost any wellbore and yet remain small enough to pass throughrestrictions while getting to setting depth.
Increased hole-size efficiency. Wells can be drilled with one less casing string while still providing the samefinal well diameter.Typically,an ESS final internal diameteris only 1 in.less than the borehole diameter it was set in.
Increased productivity through skin effect reduction. In several wells,the ESS has increased productivity by reducing skin effects.Forinstance,in a Dutch gas well,a 240-ft,3-in. ESS in a 57/8-in. open hole produced with a skin factor of?0.8.Likewise,an Oman oil well with a 40-ft.,4-in.ESS in a 7-in.cased hole produced with a skin factor of 0.0.These improvements in inflow performanceare due to the system’s ability toreduce plugging tendency,thus minimizing pressure drops across the filter and wellbore interface.
Reduced pressure drops in open and cased-hole. In open-hole applications,the ESS supports the formationand prevents sand particles from leavingthe wellbore face,minimizing finesmigration and any resultant screen plugging.A further benefit of borehole support and elimination of the annulus is that mud cakes can be backproduced,avoiding intermixing with formationsand in an open annulus.Intermixingcan lead to a low-permeability filtercake on the screen and increased pressure drops.
In cased-hole applications,studieshave shown that reducing length of theflow path from reservoir to screen reduces pressure drops.In a casedhole ESS application,the screen isplaced directly against the perforationtunnel entrance.This eliminates thepressure drop component present inthe packed casing/screen annulus,again leading to reduced system pres-sure drops and improved production performance.
Cost efficiencies. ESS technologycan have signif icant cost-cutting effects in situations such as multiplelayered reservoirs,where internal gravel packs traditionally have beenapplied.For instance,while introduc-ing the technology to its operations,in stages,one offshore Borneo(Kali-mantan)operator employed 200 ft of4-in.ESS in a well while simultaneously deploying a gravel pack aboveit.Although no comparative production data is yet available,the ESS installation costs were a fraction ofthose of the gravel pack.
Remedial installations. Unlike conventional well screens,the new tech-nology has the maximum possible circumferential area and no blank areas(even at connections),thus providing maximum flow for optimum production and less chance of plugging.Itsremedial use is especially useful in multiple-zone completions,where only oneintermediate zone may require sandcontrol.
Case histories. Petroline commercially launched the ESS System inlate 1999.The technology has been deployed in reservoirs in Europe,the Middle East,Asia Pacific,Latin America and Nigeria,with open-hole andinternal gravel pack replacementsbeing the two most widely used ESS applications.
World’s first horizontal application. The most recent and noteworthy of these deployments is the successful installation and expansion in a Nigerianwell of more than 1,130 ft of 4-in.ESSin the first-ever horizontal application ofthe technology.The well flowed at 1,243bopd with a PI of 1.195 bpd/ft.Thiscompares well with the field average of0.65 bpd/ft in wells in which conventional screens were deployed.
World’s first semisubmersible installation. A major North Sea operator,in the world’s first semisubmersible ESS installation,deployed 438 ft of 51/2-in.ESS into 81/2-in.open hole at 10,558ft,at 76°deviation.An earlier well inthis field used conventional screens andproduced sand almost immediately after completion.The ESS was chosen toallow comparison with traditional sandcontrol technology.
This job also included f irst-everdeployment of the Expandable IsolationSleeve(EIS),which is similar to aninflatable packer,but does not needinflation fluid.An EIS has an ID/ODratio of 0.85,compared to a typical ratioof 0.65 for an inflatable packer.The EIS was used to isolate the upper section of the borehole from unwanted flow.
During cleanup,the well was beaned up,using a step-rate sequence,to aneventual rate of 53 MMscfd at 1,583-psi WHFP.No sand production was seen throughout the flowing period.There was evidence?via BS&W samples col-lected at surface?of the filtercake being backproduced,as per plan.The well’spotential will be reached once it is fullycommissioned via the production facil-ities.Initial indications are that overallwell performance is better than expected.
Future applications. In first-quarter2000,ESS applications will include alarge campaign of cased-hole applica-tions in multi-layered reservoirs,which will take place offshore Borneo(Kali-mantan).Several horizontal applications exceeding 2,000 ft in length are scheduled in the UK Atlantic Frontier region and offshore China.A 1,600-ft horizontal application is also planned for the deepwater region offshore Brazil.
杨宝剑 是振威(全球)石油网的高级技术编辑,在石油技术资讯行业有八年的学识和经验。他源源不断地提供石油行业全球最新的技术创新、研发成果、现场应用情况等信息。如果你对“新技术新产品”的内容有任何问题或建议,请联系杨宝剑编辑 +86 10-58236512 Email:allenyo@zhenweiexpo.com 欢迎您提供手中的最新技术文章!